-
Quality Assurance

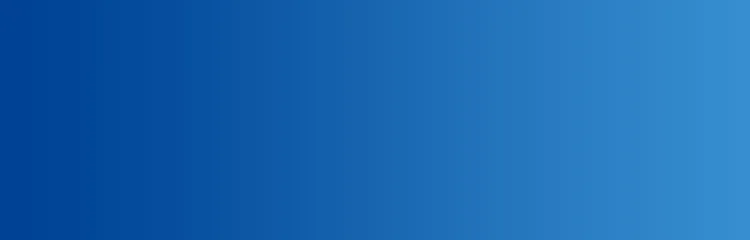
Quality Assurance
JDI strives to build a relationship of trust with its customers through careful and respectful communication, and to ensure that all departments involved in JDI’s product planning, design, manufacturing, sales, and service understand customers’ needs and provide products and services that meet those needs.
Quality policy
- To provide satisfying quality to customers in accordance with Our Mission.
- To be responsible for our quality, act with speed and honesty, and make further improvements.
- To be compliant to requirements and continually improve the quality management system.
Quality Assurance Activities
Based on our quality policy, JDI has established a quality management system. All departments are running the PDCA (Plan Do Check Action) cycle and continuously improving with the cooperation of our business partners. JDI has also enhanced our customer support system to connect customer feedback to improvements. In providing new products, JDI verifies performance and reliability that meet customer requirements at the product development stage before transitioning to mass production. At the mass production stage, JDI monitors the quality of components and manufacturing processes. If defects are detected, JDI uses advanced analysis techniques to identify the root cause, ensures measures are implemented, and maintains and ensures the quality of shipped products.
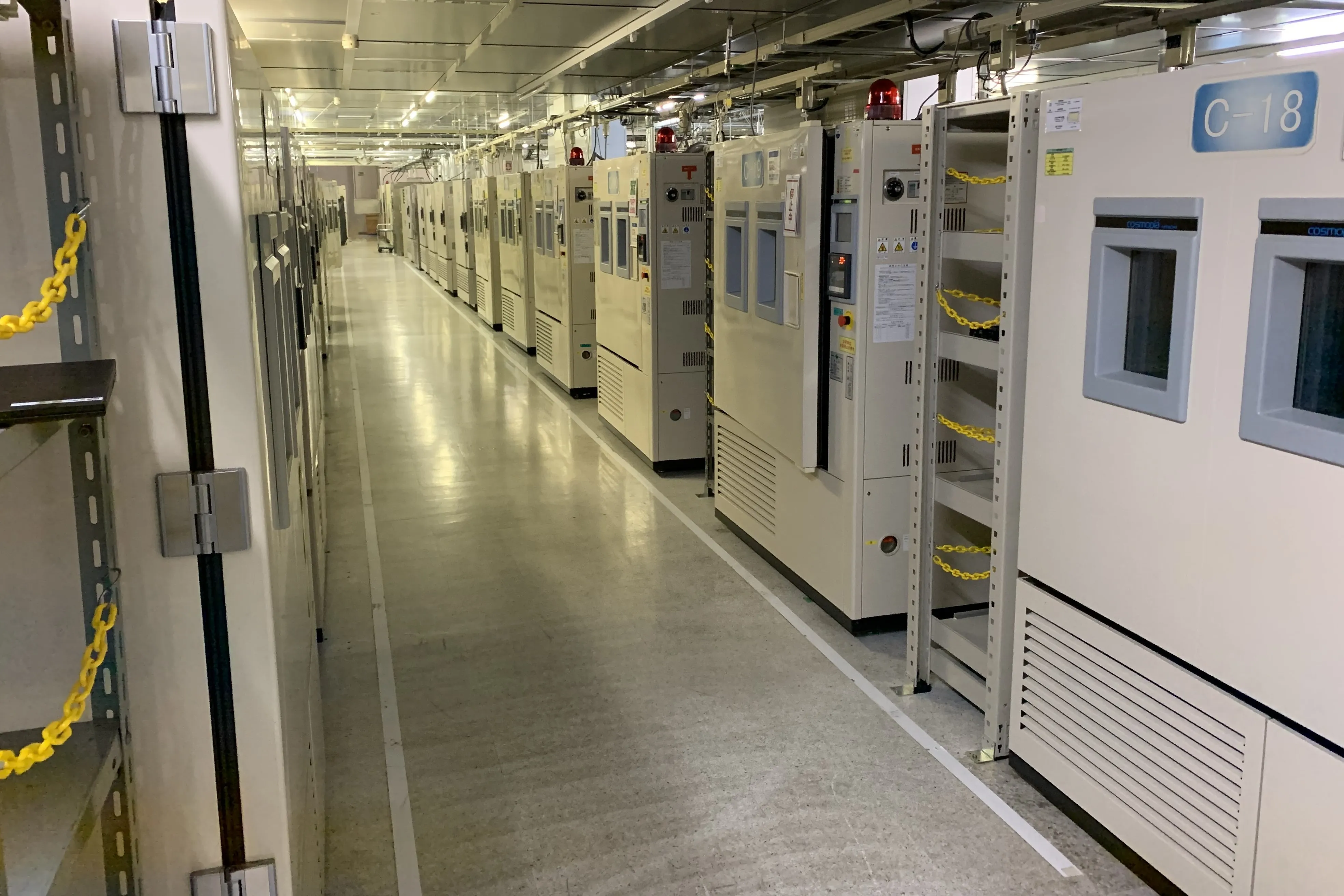
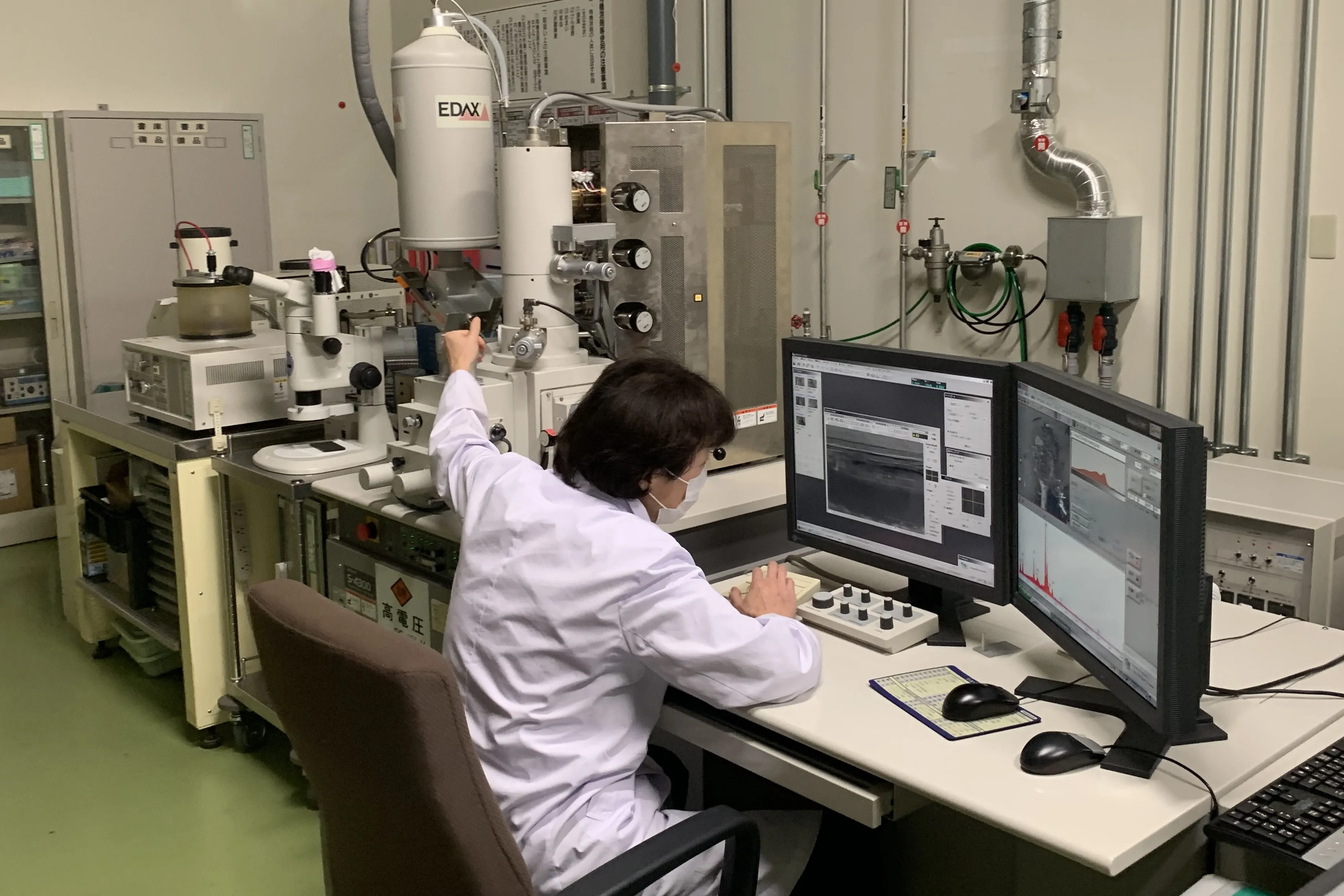
Quality Assurance Guidelines for Business Partners
This is a compilation of matters for which JDI requests understanding and cooperation from our business partners regarding our quality management system.
ISO 9001 and IATF 16949 certifications
JDI is ISO9001:2015 certified. In addition, our sites related to automotive displays are IATF16949:2016 certified.